Use-case oriented vehicle manufacturers expand niches
The last few years have clearly shown us the changes we are undergoing socially and economically. Global warming, the Corona crisis and armed conflicts in Europe have shaken long-standing principles. At the same time, international competitive pressure is increasing, putting the automotive industry under pressure to act. On the one hand, vehicle manufacturers must invest in order to position their companies for the future, but at the same time they must remain competitive.
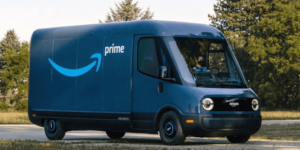
In addition to the existing automotive OEMs, use-case oriented vehicle manufacturers are currently becoming increasingly established. These suppliers do not serve a mass market, but develop and sell vehicles to meet specific requirements. From municipal vehicles to craftsmen’s vehicles or new urban vehicles, new solutions are emerging for individual requirements.
For example, Streetscooter, a company based in Aachen, Germany, has successfully established a customized product on the market with customized electric delivery vans for the German postal service. In September 2022, Amazon’s investment in Rivian also made headlines. The cooperation with the eCommerce giant even led Mercedes-Benz to join the project.
In this context, some recurring characteristics emerge among use-case oriented vehicle manufacturers:
- Lightweight construction approaches: To reduce vehicle emissions, lightweight materials are increasingly being used to achieve resource-saving mobility. At the same time, simplified registration requirements for lightweight vehicles can save a great deal of bureaucratic effort.
- Low volumes: Use-case optimized vehicles serve niche markets and are therefore hardly suitable as a business case for corporations oriented toward mass markets. Small and medium-sized companies, on the other hand, can shine with their niche expertise, agility and customer orientation, even with low volumes.
Challenges and solutions for low-volume vehicle manufacturers
There are a number of challenges for this new generation of new vehicle manufacturers. For example, lightweight construction requires in-depth knowledge of materials, simulation methods and new production methods. But the low volumes of the solution providers are also challenging. Economies of scale, as in the mass production of large automotive series, can only be achieved to a limited extent. As a result, the vehicles are often barely competitive in terms of price and face a wide range of technical challenges.
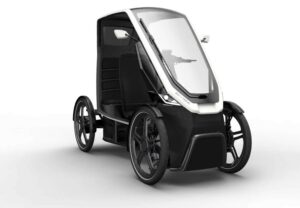
A current example of such a failure is Schaeffler’s Bio Hybrid. The nimble urban transporter was clearly ahead of its time. Narrowly built, weather-protected, and with sufficient transport volume, it was intended to supply large cities flexibly and with low emissions. On the other hand, customer benefits and costs of just under EUR 10,000 for a cargo bike were probably not quite in proportion. In the summer of 2021, after several years of development and changes of ownership, the project and the company were dissolved.
So there is a need to provide small vehicle manufacturers with tools and opportunities to successfully bring their products to market. This concerns both the production and the efficient development of the vehicles.
Development and manufacturing platforms converge
Targeted organizational measures can be taken to achieve economies of scale comparable to those in high-volume production. In manufacturing, manufacturing platforms offer a decisive lever in the realization of low costs through the bundling of orders. This is because, in contrast to individual orders for components from manufacturers, larger order volumes and better conditions can be achieved by combining several orders. Particularly in the case of medium series sizes, which are common for individual mobility solutions, we at InstaWerk save our customers over 20% in component costs and almost 90% in ancillary procurement costs during CNC production. This is made possible by our instant ordering for CNC-manufacturing, our digital processes and our international network of manufacturers.
However, development must also be made more efficient, because the high complexity of the vehicles requires a high level of investment in development, testing and certification of the vehicles. International cooperation, clear development processes and targeted management of the development processes can help here.
But there is also cost potential to be leveraged at the interfaces between development and production. This was one of the main reasons for us at InstaWerk to participate in the IntWL research project of the German Federal Ministry of Economics and Climate Protection. In a consortium of 25 project participants, a digital development and production platform for small and medium-sized enterprises is being set up, which will enable manufacturing companies and engineering service providers in cooperative approaches to offer complex products in small quantities and thus increase their global competitiveness. Distributed development and production dramatically lowers the barriers to entry in the form of upfront investment. A fundamental increase in project efficiency allows development cycles to be drastically shortened and reduces costs. Small companies could thus become integrators or OEMs themselves.
We are certain that the development of the platform economy in manufacturing will soon extend to engineering. For years now, there has been a shift of commodity engineering services to the Asian region and a higher specialization of engineering providers in Europe in complex, knowledge-heavy services. Digitization will significantly simplify the more efficient utilization of these resources and their integration into the overall development process. Our task will be to help shape and define this digitization, rather than being overwhelmed by a wave of digitization.
At InstaWerk, we will continue to work on making CNC manufacturing available to our customers in a simple, efficient and high-quality way, thus contributing to the competitiveness of small mobility providers.