A History of Manufacturing Systems
The modernization in manufacturing processes has significantly changed owing to the ever-increasing global competition, globalization of manufacturing resource and rapid development of advanced level manufacturing technologies.
The key objectivity of manufacturing has shifted in the last decades: From mass production i.e. expansion of production scale in the 1960s, to minimizing production expenses in the 1970s, to strategies utilized in promoting quality of product in the 1980s. In the 1990s significance was given to immediate market responsiveness followed by the growing emphasis laid upon knowledge enhancement and consumer service in the 2000s. Since 2010 a strong trend towards digital supply chains can be observed, which will be studied in detail in this article. A wide range of manufacturing models and methodologies have been proposed in order to meet the objectives of TQCSEK i.e. fastest Time to consumer market, best Quality, Cost Effective, finest Service, Environmentally friendly, and high degree Knowledge.
Computer Integrated Manufacturing (CIM) incorporates intelligent systems i.e. machines, robots, computer systems/databases to regulate the overall manufacturing and production process. The integration of software based systems to the manufacturing process allows individual units to exchange the information and initiate or terminate actions within the production framework. Hence, CIM allows faster and efficient (low error margin) manufacturing with the main advantage being the automation of production line and creation of products without labor intensive approaches.
Agile Manufacturing (AM) is a manufacturing principle where an organization creates the processes, equipment and a skillful trained workforce which generates prompt responsiveness to consumer demand and market changes while simultaneously regulating manufacturing cost and quality standards. The motivation behind an organization becoming an Agile Manufacturer is the establishment of manufacturing support technologies allowing marketing individuals, designing and production personnel to share a common platform i.e. database system, incorporating inventory stock (spare parts and products) thus allowing data sharing and exchange on the running production capacity and issues pertaining to the smaller initial low-end faults which may give rise to downstream effects of larger intensity.
Concurrent Engineering (CE) is an engineering approach, where multiple factors relevant to the product’s life cycle are considered during the initial prototype design stages with emphasizing the parallelization of tasks to safe time. The factors considered in CE include the functionality of the product, the manufacturing process, assembling of product according to design specifications, testing of prototype developed, maintenance, reliability, cost factor i.e. cost effectiveness and the standard of quality. The main essence of CE is not specifically making the manufacturing stages concurrent, but it incorporates the overall cumulative effort by the units involved in making the process cost effective and competitive.
Networked Manufacturing (NM) forms its basis using the internet as a main source of complete sharing and joint management of resources employed in manufacturing process with the resource distribution in several different locations.
The above-mentioned manufacturing models and techniques incorporate a unique perspective and significance thus playing a vital role during the advancement and growth of the manufacturing industrial sector. However, these manufacturing methods are still at early stages of industrial manufacturing due to many bottlenecks involved in terms of implementation on a larger scale. These bottlenecks include:
- Uncertainty involved in delivering an efficient, high quality and time-bounded i.e. on time service delivery (raw material to finished products and troubleshooting)
- Proper allocation of resources i.e. unavailability of resource sharing mechanisms
- Non-existence of intelligent embedded computational framework, i.e. Artificial Intelligence (A.I) based automated synchronization of manufacturing processes.
- Issues of free circulation and cooperation of the resources and capabilities incorporated in the manufacturing process arise
For instance, the Networked Manufacturing (NM) mechanism does achieve a certain level of resource sharing. However, the resources shared are limited to the internal framework of the corporation. In the current scenario, one of the main challenges in the promotion and application of the manufacturing network model is the ability to share the available manufacturing resources and capabilities with a higher frequency in a much wider range with the realization of a barrier-free distribution and transaction of the manufacturing and production resources, and capabilities in order for their utilization to be on demand i.e. On demand Manufacturing. Only upon achieving the barrier free resource transaction and circulation, and the on-demand usage of manufacturing resources can the realization be made of the transition from a production-oriented manufacturing to service oriented manufacturing.
Transition from Product Oriented Manufacturing to Service Oriented Manufacturing
The current era of globalization has led to the transition of large manufacturing processes in particular from mass production of goods and services to mass customization thus allowing industries to adapt and succeed in newly emerging competitive markets. The survival of industries in the manufacturing sector is dependent upon the integration of their product research and development stages and the manufacturing processes globally. Globalization has also allowed the suppliers to distribute the goods and services on a geographic scale on a global basis.
In order to fulfill the developmental process for attaining finished products, the aggregation of process resources becomes essential. To address the arising challenges pertaining to globalization, a great amount of development has been done to incorporate software based solutions comprising of Grid Manufacturing, Service Oriented Manufacturing (SOM), Product-Service Manufacturing Systems, and Cloud Manufacturing. The Merits of the provided solutions pertaining to CIM – Computer Integrated Manufacturing cannot be ignored, but the issue lies in the CIM solutions being highly product oriented.
It is a common belief that in order to maximize profit and revenue generation in conjunction to maintaining the competitive advantages, the shift from a product oriented to service-oriented systems approach becomes inevitable. The transition to service-oriented systems are based on the proposition requiring incorporation of the definite processes in order to achieve added value via combination of both services and product-oriented system frameworks.
A Brief Review on Cloud Manufacturing
The arise of a new service-oriented model i.e. Cloud Computing was introduced to the market and applied on a larger scale in various sectors. The main objective of Cloud Computing is to use the computer data storage infrastructure and the computing services by a third-party service provider thus allowing storage and processing of data in the “Cloud”. Considering the IT perspective, the Cloud Computing is a continuation of the virtualization (VM) and Grid Computing (MGrid). Large enterprises including Google, Amazon, IBM, NVIDIA etc. have invested a great deal of capital and workforce in order to provide cloud based architectures and services to their customers.
Cloud Manufacturing is a manufacturing strategy based on service-oriented manufacturing (SOM) principles allowing global sharing of manufacturing resources at a larger scale. Cloud Manufacturing is integrated with advanced software based systems, including Cloud Computing, Internet of Things (IoT), virtualization and Artificial intelligence (A.I). Cloud Manufacturing aggregates global manufacturing resources and makes them available over digitally accessible user interfaces. Through integration of the large scale, varied and scattered manufacturing resources, the Cloud Manufacturing framework establishes a vast array of manufacturing resource accessible to companies, increasing cost-efficiency, establishing resilient supply chains and improving customer-orientation and agility.
The basic concept of Cloud Manufacturing
Cloud Manufacturing can be described as a recently developed manufacturing strategy which is based on networks and platforms. It incorporates different networks, cloud computing and manufacturing processes to transform manufacturing resources and capability into a “manufacturing services” i.e. manufacturing as a service (MaaS). The goal is to make available resources both manageable and operatable in a coherent and intelligent manner thus allowing the complete sharing and circulation of incorporated manufacturing resources and capabilities. Therefore, Cloud Manufacturing platforms like InstaWerk can provide a very safe, reliable, great quality, cost effective and an on demand manufacturing service.
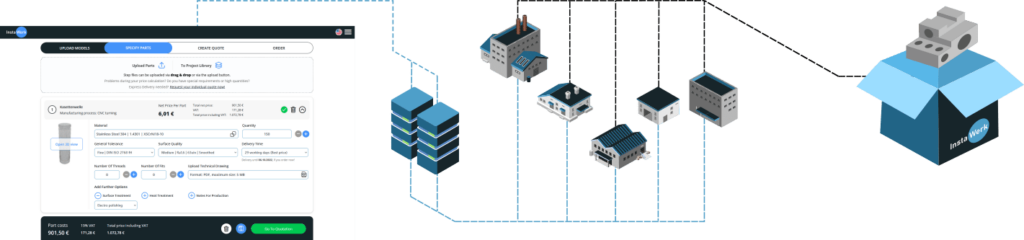
The cloud manufacturing operator ensure an efficient management system and the uninterrupted operation of cloud services. The services within the cloud are provided via various service providers based upon the providers’ overall manufacturing resources and capabilities. The vast number of cloud services by the service providers are collated and integrated into a single overall manufacturing cloud as per the cliental requirements with regards to the manufacturing process. The overall manufacturing life-cycle’s process including different services are provided by the manufacturing cloud. The service users are authorized usage of various dynamic application services according to the on-demand principle along with the Cloud Manufacturing operation platform’s support and the realization of the multi-agent platform’s collaborative interaction.
The Knowledge platform has a vital central support role during the overall functionality of the Cloud Manufacturing process. Within the Cloud Manufacturing system framework, the knowledge-based integration becomes achievable across the overall life cycle of manufacturing. The knowledge platform is not limited to providing support to the virtualization access, and the service-oriented encapsulation of the resources and capabilities incorporated in the overall manufacturing life cycle, but it also supports the realization of the cloud service(s) based functionality i.e. organized management system, intelligent search platforms, logistics etc.
The Architecture of Cloud Manufacturing Systems
The overall architecture (system composition) of the Cloud Manufacturing consists of five main layers or categories including the Ressource-Layer, Perception-Layer, Service-Layer, Middleware-Layer, and Application-Layer respectively.
The Resource layer (R-Layer) comprises of the manufacturing resources employed and capabilities layer. Manufacturing resources are further categorized into hard manufacturing resources (machining tools, simulation, and experimentation equipment etc.) and soft manufacturing resources (Design for Manufacturability (DfM) simulation, data, software and knowledge base). The formation of Manufacturing capabilities occurs with resources, people or corporations, and knowledge which allow the completion of individual manufacturing tasks or any experimentation with a background support of resource employed in manufacturing, and the knowledge incorporating design attributes, modelling and simulation capabilities, product capabilities and other capabilities relevant to the overall manufacturing process life cycle.
The Perception (P-Layer) incorporates sensing physical manufacturing resources and capabilities, allowing their linkage to the cloud network, and the processing of relevant data and information via utilizing technology platforms such as RFID, IoT etc. in order to realize the complete connection of different resources and capabilities incorporated in the manufacturing process.
The Service (S-Layer) includes Cloud Manufacturing’s virtual resources and services which are mainly responsible for virtualizing and encapsulating the overall manufacturing resources and capabilities to relevant cloud services and henceforth leading to formation of services pool.
The Middleware (M-Layer) mainly delivers the core functions and the service-based support mechanisms for continuous operation of the Manufacturing Cloud including the Management of Cloud service, knowledge management, managing cooperation, managing the platform running without bottlenecks, transaction management, management of arising failures, management of overall energy utilized in manufacturing life cycle etc.
The Application (A-Layer) ensures the applicability of Cloud Manufacturing based fields of manufacturing and industries which provide different specified application interface(s) and relevant equipment categorized as end-interaction. Various users are allowed access to the cloud service in the Cloud Manufacturing system as per demand or requirement.
The Main Specifications of the Cloud Manufacturing System
The main Characteristics of Cloud Manufacturing can be categorized into four subcategories:
- Providing on-demand manufacturing services during the product life cycle: From prototyping to mass production
- Supporting agile organizations by providing flexible machining ressources and freeing internal resources for customer-oriented services
- Intelligent insights into the manufacturing resources and improving resilience
- Intelligent Manufacturing by matching customer requirements to available manufacturing resources
In addition to manufacturing resources, a complete range engineering and service capabilities pertaining to the overall manufacturing life cycle are provided to the users of the service including “Design as a Service” (DaaS), “Manufacturing as a Service” (MFGaaS), “Experimentation as a Service” (Eaas), Simulation as a Service” (SImaaS), “Logistics as a Service” (LaaS), “Assembly as a Service” (AaaS) etc. The complete range of the aforementioned services are utilized on-demand along with the scalable service platform’s support framework.
The Cloud Manufacturing framework provides users with the ability to construct various virtual corporations as per their specifications. The manufacturing platform provides an overall support to associated tasks and processes being utilized during design and operation of virtual organizations.
Cloud Manufacturing brings in soft and hard resources employed in manufacturing. It makes particularly hard manufacturing resource accessibility (i.e. machining tools and centres, modelling and simulation equipment, testing apparatus, logistic goods, and services etc.
Startups, SMEs, institutions, enterprises etc. can become a part of discussion thus contributing their manufacturing resources, capabilities, and knowledge to the Cloud Manufacturing Platform. The manufacturing activities pertaining to any associated individual or enterprise can be carried out based on these manufacturing resources, capabilities, and knowledge.
InstaWerk as an on-demand Manufacturing Solution for CNC manufacturing
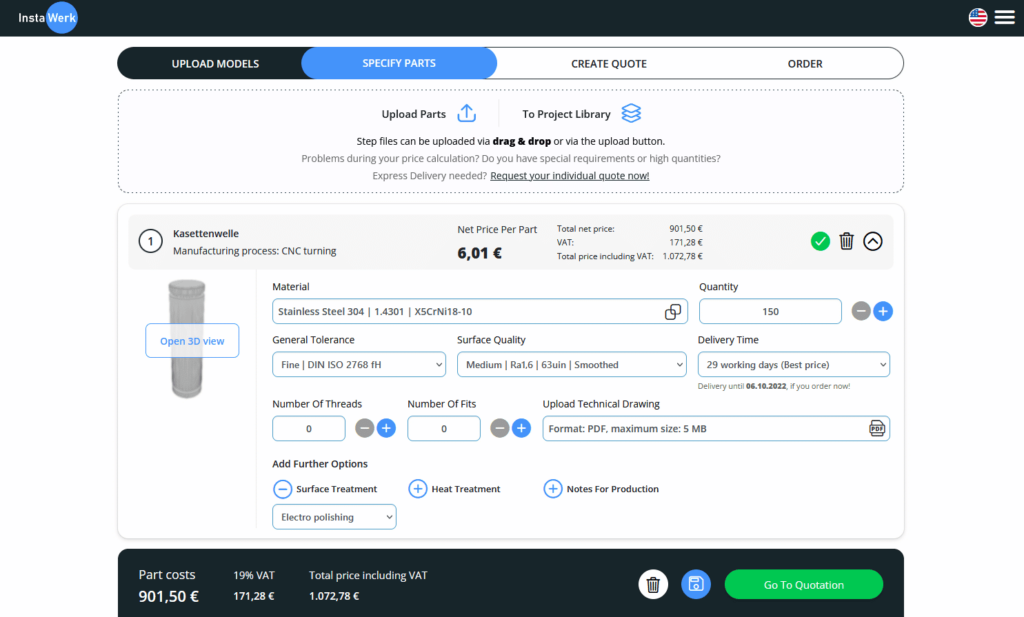
InstaWerk is a specialized provider for CNC manufacturing. We work as a cloud manufacturing solution from Germany and with a strong focus on quality and customer satisfaction. While our solutions are also rooted in theoretical foundations of software development and platform economics, our focus is on the practical usability of our solution.
Our instant pricing for CNC machining allows us to calculate costs for turned parts and milled parts in seconds, and our customers can order these parts directly. The orders are then bundled with other orders and processed in the manufacturing network. In the process, InstaWerk continuously monitors component quality and thus continuously optimizes the network for quality.
The best thing about it is that, unlike in theory, it is very simple: Just register and you can directly calculate and order your components online.
References
- A. Rymaszewska, P. Helo, & A. Gunasekaran. (2017). IoT Powered servitization of manufacturing-an exploratory case study. Int. J. Prod. Econ., 192, 92-105.
- Abdalla, H.S. (1999). Concurrent engineering for global manufacturing. International Journal of Production Economics, 60–61, 251–260.
- B.H. Li, L. Zhang, S.L. Wang, F. Tao, J. Cao, X. Jiang, . . . X.D. Chai. (2010). Cloud manufacturing: A new service-oriented manufacturing model. Comput. Int. Manuf. Sys, 16, 1–7.
- Beuren, F. H., M. G. G. Ferreira, & and P. A. C. Miguel. (2013). Product-service Systems: A Literature Review on Integrated Products and Services. Journal of Cleaner Production, 47, 222–231.
- Chen, K., & Zheng, W.M. (2009). Cloud computing: system instances and current research. Journal of Software, 20(5), 1337–1348.
- Delaram, J., & O. F. Valilai. (2016). Development of a Novel Solution to Enable Integration and Interoperability for Cloud Manufacturing.”. Procedia CIRP :, 52, 6-11.
- F. Jauro, H. Chiroma, A.Y. Gital, M. Almutairi, S.i.M. Abdulhamid, & J.H. Abawajy . (2020). Deep learning architectures in emerging cloud computing architectures Recent development, challenges and next research trend. Appl. Soft Comput., 96, 1065-1082.
- Flammia, G. (2001). Application service providers: challenges and opportunities. IEEE Intelligent Systems and Their Applications,, 16 (1), 22–23.
- H. Xu, X. Qiu, W. Zhang, K. Liu, S. Liu, & W. Chen. (2021). Privacy-preserving incentive mechanism for multi-leader multi-follower IoT-edge computing market: A reinforcement learning approach,. J. Syst. Architect., 114, 1019-1032.
- He, W., & Xu, L. D. (2015). A State-of-the-Art Survey of Cloud Manufacturing. Int. J. Comput. Integr. Manuf.,, 28(3), 239–250.
- Kalpakjian, S. , & Schmid, S. (2006). Manufacturing engineering and technology (5th ed., Vol. 1192). New Jersey: Prentice Hall.
- Kazuaki, I. (1997). Virtual manufacturing systems as advanced information infrastructure for integrating manufacturing resources and activities. CIRP Annals-Manufacturing Technology, 46(1), 335–338.
- Kumar, S., Kadow, B.B., & Lamkin, M.K. (2011). Challenges with the introduction of radiofrequency identification systems into a manufacturer’s supply chain-a pilot study. Enterprise Information Systems, 5(2), 235-253.
- Laplante, P.A. (2005). Comprehensive dictionary of electrical engineering (2nd ed., Vol. 136). USA: CRC Press.
- Li, B.H. (2010). Cloud manufacturing: a new service-oriented manufacturing model. Computer Integrated Manufacturing Systems, 16(1), 1-8.
- Li, B.H., Chai, X.D., & Hou, B.C. (2009). Networked modeling & simulation platform based on concept of cloud computing—cloud simulation platform. Journal of System Simulation, 21(17), 5292–5299.
- Lin Zhang, Yongliang Luo, Fei Tao, Bo Hu Li, Lei Ren, Xuesong Zhang, . . . Yongkui Liu. (2014). Cloud manufacturing: a new manufacturing paradigm. Enterprise Information Systems, 8(2), 167-187. doi:10.1080/17517575.2012.683812
- Matt, D. T., E. Rauch, & P. Dallasega. (2015). Trends Towards Distributed Manufacturing Systems and Modern Forms for Their Design. Procedia CIRP, 33, 185-190.
- Meier, H., Volker, O., & Funke, B. (2010). Industrial Product-Service Systems (IPS2) paradigm shift by mutually determined products and services. International Journal of Advanced Manufacturing Technology,, 52(9-12), 1175-1191.
- Montreuil, B., Frayret, J.-M., & D’Amours, S. (2000). A strategic framework for networked manufacturing. Computers in Industry, 42 ((2-3)), 299–317.
- Ning, H.S., Zhang, Y., & Liu, F.L. (2006). Research on China Internet of things’ services and management. Acta Electronica Sinica, 34(12), 2514–2517.
- Park, K.H., & Favrel, J. (1999). Virtual enterprise-information system and networking solution. Computers & Industrial Engineering, 37, 441-444.
- Preiss, K. (1994). Agile manufacturing. Computer-Aided Design, 26(2), 83–84.
- Rising. (n.d.). Retrieved from http://security.zdnet.com.cn/security_zone/2009/0728/1419875.shtml
- Shen,W., Q. Hao, S.Wang, Y. Li, & H. Ghenniwa. (2007). An Agent-Based Service-Oriented Integration Architecture for Collaborative Intelligent Manufacturing.”. Robotics and Computer-Integrated Manufacturing, 23(3), 315–325.
- Smith, A.D., & Rupp, W.T. (2002). Application service providers (ASP): moving downstream to enhance competitive advantage. Information Management and Computer Security,, 10(2-3), 64-72.
- Tan, W.N. (2010). A methodology toward manufacturing grid-based virtual enterprise operation platform. Enterprise Information Systems, 4(3), 283-309.
- Tao, F. (2008b). Resource service composition and its optimal-selection based on particle swarm optimization in manufacturing grid system. IEEE Transactions on Industrial Informatics, 4(4), 315-327.
- Tao, F. (2009a). Study on resource service match and search in manufacturing grid system. International Journal of Advanced Manufacturing Technology, 43((3-4)), 379-399.
- Tao, F. (2010b). Study of failure detection and recovery in manufacturing grid resource service scheduling. International Journal of Production Research. 48(1), 69–94.
- Tao, F. (2011a). Typical characteristics of cloud manufacturing and several key issues of cloud service composition. Computer Integrated Manufacturing Systems, 17(3), 477–486.
- Tao, F. (2011b). Cloud manufacturing: a computing and service-oriented manufacturing model. Proceedings of the Institution of Mechanical Engineers, Part B, Journal of Engineering Manufacture, 225(10), 1969–1976.
- Tao, F. (2011b). Cloud manufacturing: a computing and service-oriented manufacturing model. Proceedings of the Institution of Mechanical Engineers, Part B,. Journal of Engineering Manufacture,, 225 (10), 969–1976.
- Tao, F., Hu, Y.F., & Zhang, L. (2010a). Theory and practice: optimal resource service allocation in manufacturing grid . 239.
- Tao, F., Hu, Y.F., & Zhao, D. (2009b). Study on manufacturing grid resource service modeling and evaluation. ,. International Journal of Advanced Manufacturing Technology, 41(9-10), 1034-1042.
- Tao, F., Hu, Y.F., & Zhou, Z.D. (2008a). Study on manufacturing grid and its resource service optimal-selection system. International Journal of Advanced Manufacturing Technology, 37(9-10), 1022-1041.
- Tao, F., Hu, Y.F., & Zhou, Z.D.,. (2009c). Application and modeling of resource service trust-qos evaluation in manufacturing grid system. International Journal of Production Research, 47 (6), 1521-1550.
- Tao, F., Zhang, L., & Nee, A.Y.C. (2011c). A review of the application of grid technology in manufacturing. International Journal of Production Research, 49(13), 4119-4155.
- Tao, F., Zhao, D., & Zhang, L. (2010c). Resource service optimal-selection based on intuitionistic fuzzy set and non-functionality QoS in manufacturing grid system. Knowledge and Information Systems, 25(1), 185–208.
- Trend Micro. (n.d.). Retrieved from http://datacenter.chinabyte.com/168/9003168.shtml
- Valilai, O. F., & M. Houshmand. (2010). INFELT STEP: An Integrated and Interoperable Platform for Collaborative CAD/CAPP/CAM/CNC Machining Systems Based on STEP Standard. International Journal of Computer Integrated Manufacturing, 23 (12), 1095–1117. doi:doi:10.1080/0951192X.2010.527373
- Valle, S. , & Va´ zquez-Bustelo, D. (2009). Concurrent engineering performance: incremental versus radical innovation. International Journal of Production Economics, 119(1), 136-148.
- Wu, D. Z., Greer, M. J., Rosen, D. W., & Schaefer, D. (2013). Cloud Manufacturing: Strategic Vision and State-of-the-Art. J. Manuf. Syst., 32(4), 564-579.
- X. Xu. (2012). From cloud computing to cloud manufacturing, Robot. Cim-Int Manuf. , 28, 75–86.
- Xu, L. (2007). A decision support system for product design in concurrent engineering. Decision Support Systems,, 42(4), 2029–2042.
- Xu, L.D. (2011a). Information architecture for supply chain quality management. International Journal of Production Research,, 49(1), 183-198.
- Xu, L.D. (2011b). Enterprise systems: state of the art and future trends. IEEE Transactions on Industrial Informatics, 7(4), 630-0640.
- Xu, W., Wei, Y., & Fan, Y. (2002). Virtual enterprise and its intelligence management. Computers & Industrial Engineering,, 42, 199-205.
- Xu, X. (2012). From Cloud Computing to Cloud Manufacturing. Rob. Comput.-Integr. Manuf., 28(1), 75–86.
- Yusuf, Y.Y., Sarhadi, M., & Gunasekaran, A. (1999). Agile manufacturing: the drivers concepts and attributes. International Journal of Production Economics, 62(1-2 ), 33–43.
- Zhang, L., Mai, J. G., Tao, F., Luo, Y. L., & Ren, L. (2014). Development Status of Cloud Manufacturing in China,” ASME Paper No. MSEC2014-4019.
- Zhang, Y. (2011). A new method for automatic synthesis of tolerances for complex assemblies based on polychromatic sets. Enterprise Information Systems, 5(3), 337-358.